Le lancement d’un nouveau produit dans l’industrie du soin et de la cosmétique est généralement associé à 5 principales étapes :
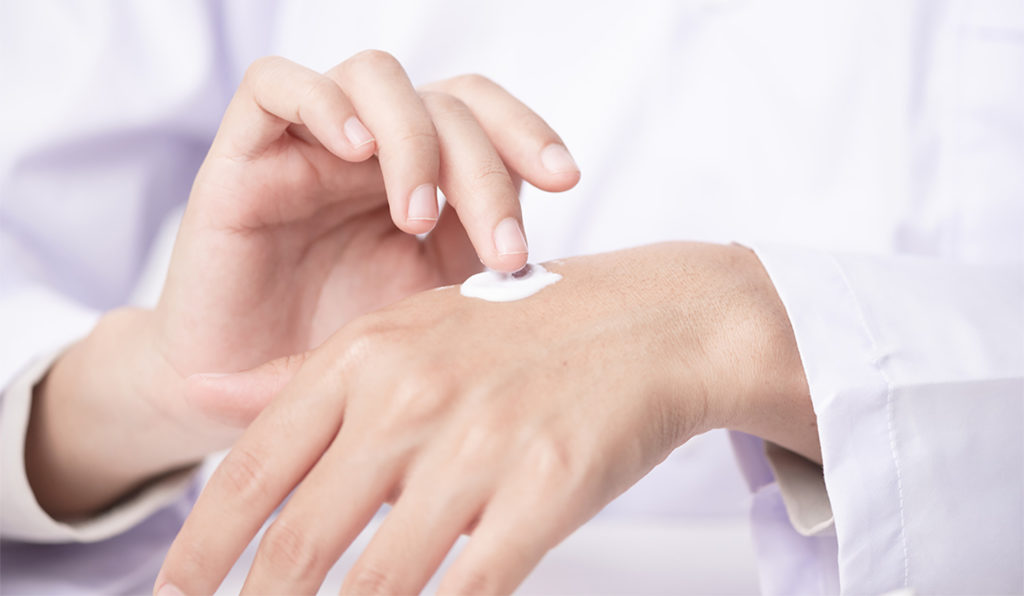
- L’identification des ingrédients et des matières premières
- Le développement de la formulation en laboratoire
- L’objectivation, avec une série de test : in vitro, ex vivo, tolérance, tests cliniques, tests consommateurs…
- La réglementation : valider la conformité du produit et procéder à son enregistrement. Selon le pays de mise sur le marché, cette étape peut considérablement allonger la durée du projet.
- La commercialisation : importateurs, distributeurs, détaillants, vente en ligne…
Toutefois, une 6ème étape capitale ne doit pas être négligée : la phase process. Cette phase intervient entre la formulation et l’objectivation. Elle inclut la détermination des éléments qui permettront la fabrication du produit : équipement, géométrie des outils de mélange, paramètres process (vitesse, temps, température, vide…), données de stérilisation et nettoyage ou encore l’extrapolation.
Le process est une variable essentielle lors du développement d’un nouveau produit car des enjeux économiques et de sécurité en dépendent :
- La qualité du produit fini : obtenir le même résultat que celui élaboré à l’échelle du laboratoire
- La sécurité, pour les opérateurs en production et pour le consommateur final
- La mise sur le marché du produit
- Les rendements de production : temps de fabrication, consommations d’énergie, d’eau, de détergents…
Les grands principes et enjeux du process de mélange
Le mélange est une opération unitaire présente dans les procédés de transformation. Elle consiste à réunir plusieurs composants pour produire un ensemble homogène. L’opération permet de mettre en contact les ingrédients et favoriser les transferts de chaleur, de matière, de quantité et de mouvement selon l’application.

L’opération apporte une énergie mécanique, qui vient augmenter l’homogénéité et diminuer la ségrégation du mélange. Selon le niveau d’exigence d’homogénéité du fabricant, un mélange réussi s’analyse selon :
- La concentration uniforme du mélange, depuis n’importe quel échantillon
- L’échelle de ségrégation spécifique : mélange homogène à l’échelle macromoléculaire, nano-moléculaire, micromoléculaire…
- Un temps de mélange optimal, qui va permettre de calculer le temps de fabrication requis
Le système d’agitation mécanique
Une grande variété de technique de mélange existe, une des plus répandue est le système d’agitation mécanique (cuve agitée). 5 paramètres clés, impactant le mélange, sont à prendre en compte :
- La cuve : les dimensions et la forme du fond de cuve
- Le type et le nombre d’agitateurs
- La rotation du mobile : vitesse, régime d’écoulement (laminaire ou turbulent)
- La durée du mélange
- Les conditions physiques imposées (pression, vide, température…)
Les 5 étapes à suivre afin de réussir son mélange
Pour obtenir une bonne agitation, différents paramètres sont à prendre en compte :
- La nature du produit (liquide, poudre, solubilité…) et la rhéologie de ses fluides (viscosité)
- La dimension technique : outil d’agitation, vitesse périphérique, taux de cisaillement…
- La dimension économique : secteur d’activité, implantation géographique, niveaux de consommation (énergie, eau, temps de production…)
Etape n°1 : identifier le type de mélange à réaliser
La première étape consiste à connaître la nature du mélange à réaliser : est-ce un mélange liquide/liquide, liquide/poudre, les liquides sont-ils miscibles ou non miscibles… ?
Etape n°2 : caractérisation des ingrédients à mélanger
Après avoir identifié le type de mélange à réaliser, il faut connaître les caractéristiques et la rhéologie des ingrédients à utiliser : densité, solubilité, granulométrie, masse volumique, viscosité, cristaux, capsule, gaz…
Etape n°3 : caractérisation des outils de mélange
La bonne connaissance du type de mélange et des ingrédients en jeu permet de déterminer le flux nécessaire pour un mélange optimal : flux radial, axial, agitation rapide… La conception et la géométrie de l’outil font varier le niveau de cisaillement et de circulation.
Etape n°4 : définition des outils dans une cuve
L’emplacement de/s outil/s dans la cuve agitée impacte le taux de pompage et de cisaillement.
Etape n°5 : calcul des paramètres de mélange
La définition des précédentes étapes permet de calculer les paramètres de mélange : vitesse de rotation, vitesse périphérique, taux de circulation dans la cuve, durée du mélange.
Choisir le bon outil de mélange selon l’application et le procédé de mélange
La détermination de l’outil va dépendre du type de mélange. Il existe 4 principaux types de mélange, commun à n’importe quel secteur d’application.
Comment choisir les bons outils pour un mélange liquides/liquides miscibles ?
Dans un mélange de plusieurs liquides miscibles, l’opération doit permettre de diluer et homogénéiser les ingrédients. Pour cela, le mobile de mélange doit générer un débit de pompage important pour favoriser la circulation.
Les hélices à flux axial favorisent la circulation dans le milieu. Pour homogénéiser les liquides mais aussi la température (chauffer/refroidir), les turbines comme la quadripale, la tripale profilée et l’hélice marine sont recommandées.
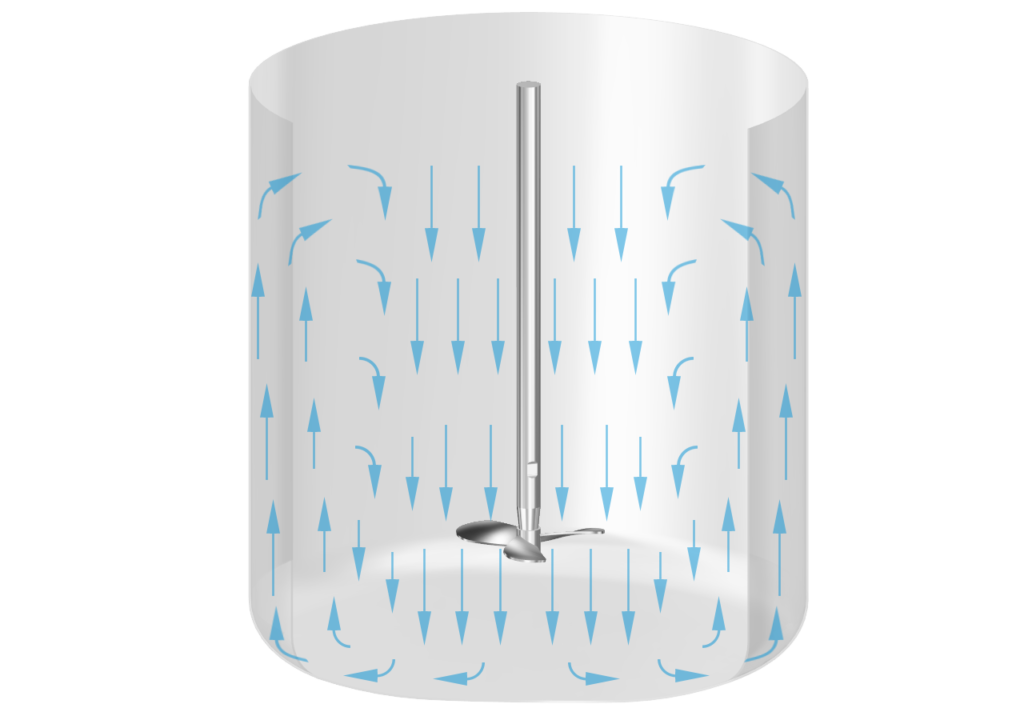
Comment choisir les bons outils pour un mélange liquides/liquides non miscibles ?
Lors d’un mélange de liquides non miscibles, la circulation ne va pas suffire pour homogénéiser les ingrédients. Le mobile de mélange doit permettre le cisaillement, pour disperser une phase dans une autre phase. Cette opération est une émulsion, procédé utilisé pour la fabrication des crèmes cosmétiques, dentifrices, baumes mais aussi des sauces dans le domaine alimentaire.
Les turbines à flux radial sont idéales pour les émulsions, ainsi que les rotors-stators.
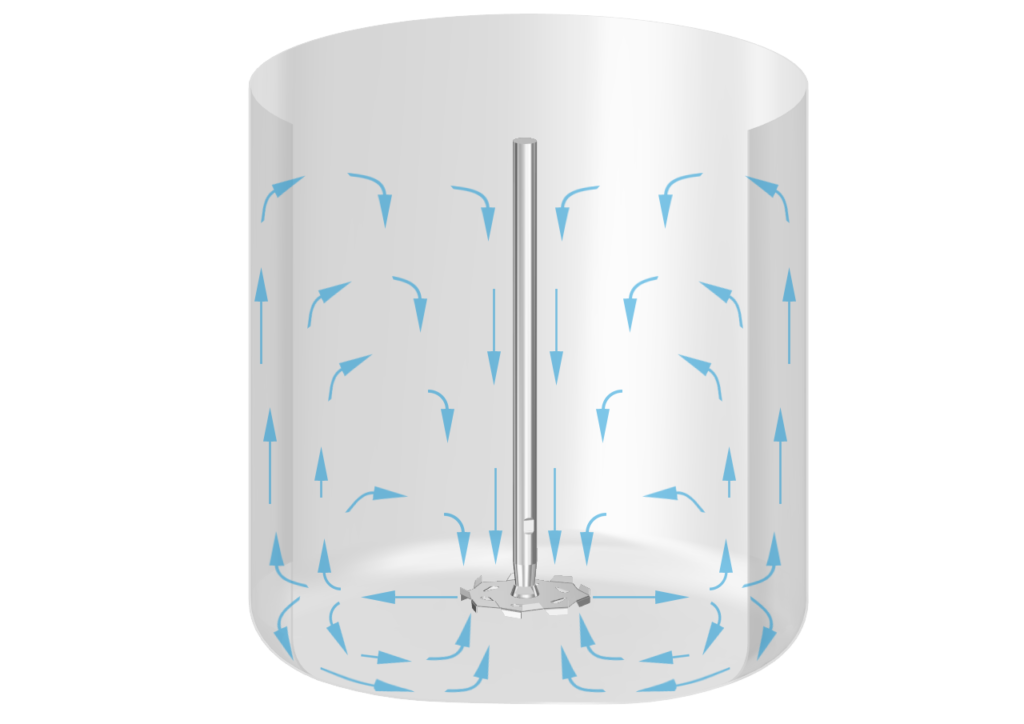
Comment choisir les bons outils pour un mélange liquides/solides ?
Les besoins varient selon les caractéristiques des particules :
- Poudres solubles : besoin de circulation pour dissoudre les particules dans le liquide
- Poudres non solubles :
- Besoin de circulation pour mettre en suspension les poudres dans le milieu (pigments par exemple)
- Ou besoin de cisaillement pour disperser les particules. Par exemple, pour la fabrication de gel, les poudres utilisées sont non solubles mais elles se transforment pendant la dispersion. Elles vont changer d’aspect et se gélifier au contact de la phase aqueuse.
Les hélices à flux axial génèrent de la circulation.
Les turbines à flux radial engendrent plus de cisaillement pour favoriser la dispersion et la transformation des particules.
Comment choisir les bons outils pour un mélange visqueux/pâteux ?
Le process de mélange visqueux est plus complexe à mettre en œuvre, il faut additionner plusieurs procédés afin d’obtenir un résultat optimal : homogénéisation, dispersion, émulsification. Dans ce cas, un seul mobile de mélange ne suffit pas. Le mobile de triple agitation Trimix intègre un émulseur pour l’agitation en fond de cuve, des hélices tripales sur 3 niveaux au centre de la cuve et un racleur. Ce mobile va permettre de fabriquer une crème hydratante liquide (13% de phase grasse) ou un baume corps plus épais (23% de phase grasse).
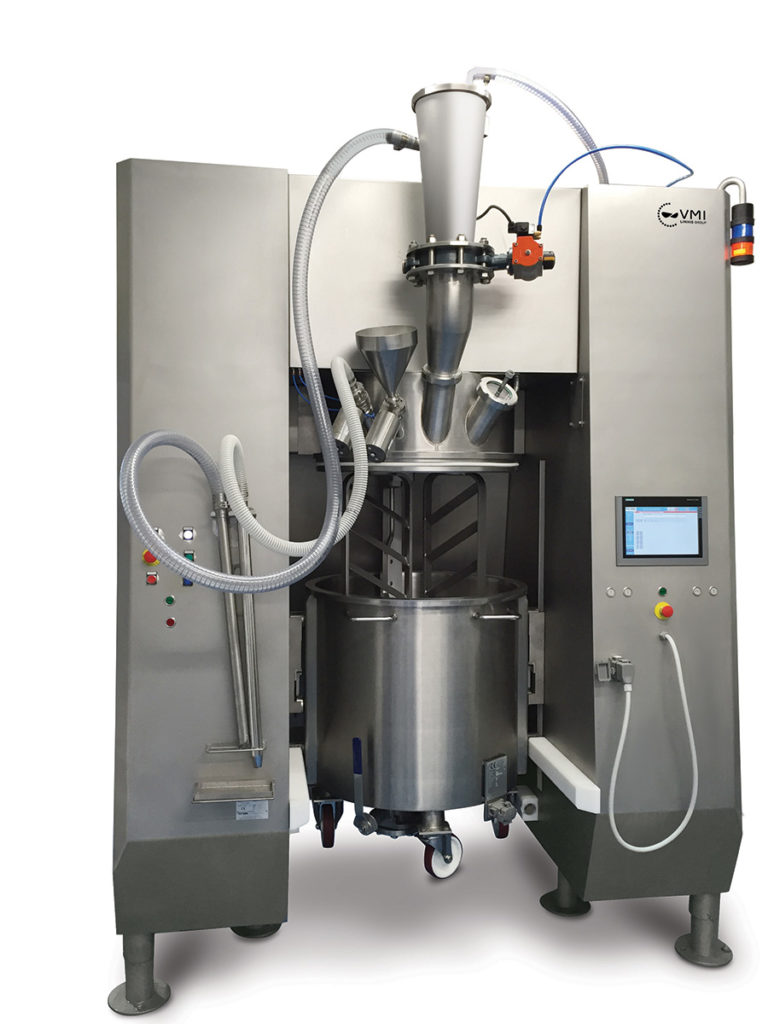
Les produits pâteux (type pommade) ont besoin de cisaillement et de circulation. Les mélangeurs planétaires sont parfaitement adaptés pour ces types de produits grâce au système de double agitation satellitaire (révolution de l’outil dans la cuve + rotation de l’outil sur lui-même).
Et pour un mélange liquide/solide/gaz…
Après l’obtention de l’émulsion, de l’air peut être incorporé pour obtenir un aspect moussant, un produit plus léger et aéré. Le mouvement de circulation permet d’incorporer l’air, et le mouvement de cisaillement réduit la taille des bulles d’air. Le mélangeur planétaire industriel Ultimix est recommandé pour ce type de mélange.
Les mobiles d’agitation peuvent être classifiés selon le niveau de viscosité des produits à mélanger.
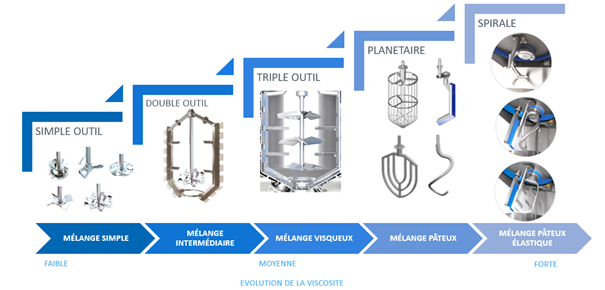
En synthèse : les critères à retenir pour choisir le mobile de mélange
Le choix de l’agitation dépend :
- Du type de flux à favoriser pour le mélange (flux axial, radial)
- Du type d’écoulement et des effets mécaniques à générer (circulation, cisaillement…)
- Des paramètres process : vitesse de rotation, taux de circulation, temps de mélange…
- Des critères fonctionnels : le type de mobile, sa nettoyabilité et son taux de rétention
- Des critères économiques : l’objectif final étant d’obtenir le meilleur rendement pour la fabrication du produit
Envie d’en savoir plus sur le choix d’un mobile de mélange?
Regardez le replay de notre webinaire « Les critères clés pour réussir vos procédés de mélange » (45 min)
Prenez rendez-vous avec un expert VMI pour obtenir des conseils process ou en savoir plus sur nos solutions de mélange.